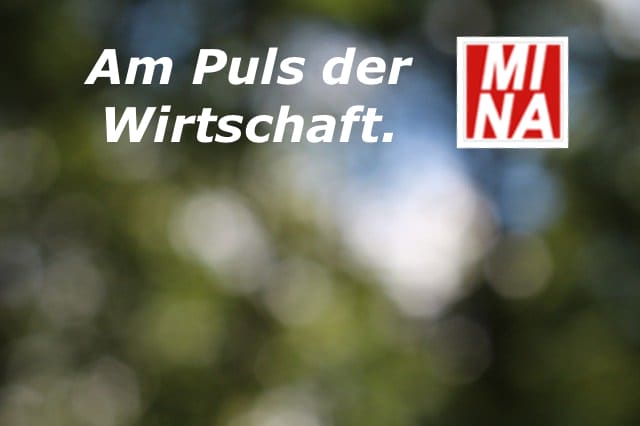
Ein Werkstück wird beim Laserschneiden mithilfe eines stark fokussierten Laserstrahls getrennt. Es werden dabei diverse Laserarten verwendet. Oft kommt ein CO2-Laser zum Einsatz, doch auch Nd:YAG-Laser werden dabei häufig verwendet. Das Funktionsprinzip besteht darin, dass ein Laserstrahl fokussiert auf das zu trennende Werkstück, oft Blech, zu richten ist. Durch den Strahl wird eine hohe Menge thermischer Energie frei. Aus der Schneiddüse strömt außerdem ein Gas, welches den Zweck hat, die Fokussieroptik vor Verunreinigungen und Spritzern zu bewahren. Außerdem hat das Gas die Aufgabe, das Material, das durch den Laserstrahl abgetragen wird, aus der Schnittfüge zu lösen. Das abgetrennte Material kann die Fuge in Flüssigkeits-, Dampfform oder als Oxidationsprodukt verlassen – je nachdem unterscheidet man zwischen drei Schneidverfahren: nämlich dem Laserstrahlschmelzschneiden, dem Laserstrahlsublimierschneiden bzw. dem Laserstrahlbrennschneiden.
Die einzelnen Verfahren
Beim Laserstrahlschmelzschneiden kommt es zur Aufschmelzung des zu bearbeitenden Stoffes in kontinuierlicher Art und Weise – dann werden durch das Gas die Abtragungen entfernt. Als Gase kommen hierbei Stickstoff und Argon zum Einsatz. Selten wird Helium verwendet. Vorteile dieses Verfahrens liegen darin, dass durch die stete Gaszuführung das Oxidieren an der Schnittfuge nicht stattfindet. Das Nachbearbeiten der Schnittkante ist somit nicht nötig. Bei den Materialien Alu, Edelstahl und Stahl wird das Laserstrahlschmelzschneiden vorrangig eingesetzt. Das Laserstrahlsublimierschneiden hat zur Folge, dass das Material in der Schnittfuge verdampft und nicht aufgeschmolzen wird. Anschließend wird es aus der Fuge herausgeblasen Das Verfahren findet Verwendung beim Schneiden von Textilien, Leder oder Holz. Beim Laserstrahlbrennschneiden wird der Stoff in der Schnittfuge auf entsprechende Temperatur gebracht, danach erfolgt die Verbrennung des Materials unter Zufuhr von Sauerstoff und das Herausblasen aus der Fuge. Der Nachteil des Verfahrens besteht darin, dass an den Schnittkanten Oxidschichten zurückbleiben. Diese Schichten müssen vor der Weiterbearbeitung mühsam entfernt werden.
Haupteinsatzgebiet des Laserstrahlbrennschneidens ist das Verarbeiten niedrig- bzw. unlegierter Stahlformen und in einzelnen Fällen von Edelstahl. Als Strahlquelle dienen meist CO2-Laser. Bei Schnittgeschwindigkeiten von 250m/min. bei Blechen unter 1mm Dicke lässt es sich rasch arbeiten.
Zu den Kosten beim Laserschneiden
Wie andere Schneidverfahren ist der Preis des Laserschneidens von diversen Faktoren abhängig. Der wichtigste ist der zu bearbeitende Stoff, Edelstahl kann kostengünstiger geschnitten werden als etwa Aluminium. Die Materialstärke hat natürlich auch einen gewissen Einfluss auf die Kosten.
Die Vor- und Nachteile beim Laserschneiden
Verglichen mit anderen Schneidverfahren wie dem Wasserstrahlschneiden bietet das Laserschneiden zahlreiche Vor- wie Nachteile. Ein wichtiger Vorteil liegt darin, dass beim Laserschneiden eine hohe Geschwindigkeit herrscht. Es ergeben sich somit kurze Bearbeitungszeiten. Beim Laserschneiden kommt es zu einer hohen Materialausnutzung, es ist ein wirtschaftliches Verfahren. Abhängig vom Werkstoff kommt es zu sauberen, schmalen Schnittkanten. Das Gravieren, Kennzeichnen und das Schneiden ist häufig mit derselben Strahlquelle und in einem Arbeitsgang möglich. Nachteil des Verfahrens ist, dass dem Stoff beim Trennen Wärme zuzuführen ist. Dadurch kommt es oft zu Gefügeveränderungen beim zu bearbeitenden Material. Außerdem entstehen hohe Anlagekosten, der Gasverbrauch ist hoch, Helium z.B. ist außerdem teuer.
Doch haben beide Verfahren ihre Vorzüge und stehen deshalb in keiner Konkurrenz zueinander, sondern bilden zusammen eine sinnvolle Ergänzung auf dem Gebiet der Fertigungstechnik.