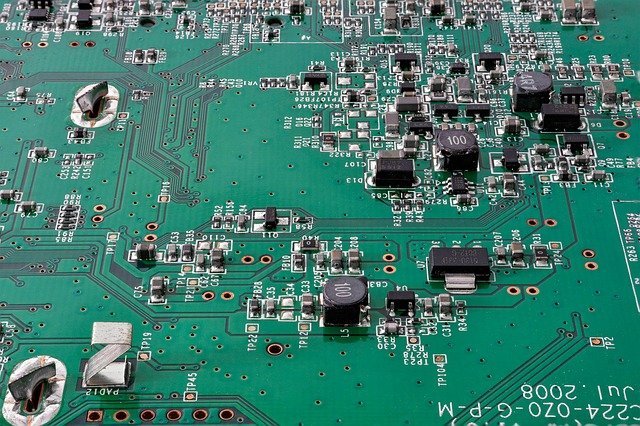
Die Leiterplattenherstellung gehört heutzutage zu den wichtigsten Teilbereichen der da nur wenige Wirtschaftszweige nicht auf die elektronischen Bauteile angewiesen sind.
Vielfältige Verwendung
Die Verwendungsmöglichkeiten von Leiterplatten sind vielfältig, verfolgen aber jeweils alle den Zweck, Daten von einer Quelle zu einem Ziel zu transportieren. Dies wiederum kann aber auf unterschiedliche Arten erfolgen, nämlich per Strom oder Signal. Zudem zeichnet sich die Leiterplatte durch ihre stabile Form aus, die dem gesamten System eine belastbare Struktur gibt.
Grundlegender Aufbau
Der Grundaufbau einer Leiterplatte besteht aus einem nicht leitenden Substrat als Grundlage und darauf angebrachten leitfähigen Bahnen, über welche der Stromfluss und damit die Datenübertragung erfolgt. Das Basissubstrat, welches für die Beständigkeit des Produkts von großer Bedeutung ist, besteht häufig aus glasfaserverstärktem Epoxidharz, das auch als Fiberglas bekannt ist. In der Praxis ist Fiberglas aufgrund seiner Korrosions- und Temperaturbeständigkeit sowie der gleichzeitig preiswerten Beschaffungsmöglichkeit sehr beliebt. Die leitfähigen Bahnen, die auch als Tracks oder Signalbahnen bezeichnet werden, werden für gewöhnlich aus Kupferblechen gefertigt. Die Auswahl der Materialien für die Leiterplattenherstellung sowie die Bestimmung der passenden Größe variieren je nach spezifischen Verwendungszweck und Einsatzgebiet der Leiterplatte.
Allgemeine Konzeption
Bevor die Leiterplatte hergestellt werden kann, muss diese vorab erst einmal konstruiert werden. Die Erstellung des Entwurfes erfolgt mittels einer individuellen Software, die mit Hilfe der angegebenen Erfordernisse eine passende Leiterplatte entwickelt. Nach der Fertigstellung des Konzepts erfolgt eine technische Prüfung auf eventuelle Fehler anhand von verschiedenen Überprüfungsalgorithmen durch einen Konstrukteur.
Individualisierte Herstellung
Der erste Teil des Herstellungsprozesses einer Leiterplatte setzt sich mit der Anfertigung des Substrats auseinander. Um eine stabile und gleichzeitig auch langfristig beständige Grundlage für die Leiterplatte zu schaffen, wird dem Aushärten des Substrats eine besondere Rolle zuteil. Nachdem das Material in die korrekte Größe geschnitten wurde, wird es über drei bis vier Stunden bei einer Temperatur von rund 150 Grad Celsius ausgehärtet. Neben der Verfestigung des Werkstoffes fördern die hohen Temperaturen die Freisetzung toxischer Verbindungen, sodass das fertige Endprodukt keine gesundheitsschädigenden Stoffe mehr enthält.
Die Ausrichtung der darauf aufzubringenden Bahnen stellt den zweiten Teil dar und erfolgt mit Hilfe einer bedruckten zweischichtigen Folie, die passgenau auf das Substrat aufgebracht wird. Sowohl die innere als auch die äußere Schicht enthalten unterschiedliche Informationen bezüglich der Aufbringung von Kupferbahnen und Stromkreisen sowie frei zu lassenden nicht leitfähigen Teilbereichen. Entsprechend der Markierungen auf den Folienschichten werden diese mit dem Leitermaterial bedruckt.
Im Anschluss daran folgt eine vollständige Sterilisation, um unerwünschte Stoffe zu entfernen, die die Leitfähigkeit negativ beeinflussen könnten, sowie die Versiegelung der Schichten. Die hierfür verwendete Chemikalie wird gemeinhin auch als Fotolack bezeichnet, da sie aufgrund ihrer hohen Reaktivität auf Licht zu einem schnellen Trocknungsprozess führt. Zum Abschluss erfolgt nach der Versiegelung eine finale Reinigung, bei der auch die Reste des nicht benötigten Fotolacks entfernt werden, und eine daran anschließende Trocknung, um Kurzschlüsse durch Feuchtigkeit zu vermeiden.
Nachhaltige Verbindung der Schichten
Die Verbindung der einzelnen Schichten der Leiterplatte stellt nochmals eine große Herausforderung dar, da hierbei ein hohes Maß an Präzision gefordert ist. Zur Qualitätssicherung wird die Leiterplatte fortlaufend optisch kontrolliert, indem ein Abgleich der ursprünglichen Konstruktion mit dem vorläufigen Produkt durchgeführt wird. Die eigentliche Verbindung der einzelnen Schichten wird durch einen Schweißvorgang erreicht. Um ein zwischenzeitliches Verschieben der einzelnen Schichten zu verhindern, werden diese durchgestanzt und mittels Stiften an einem festen Untergrund montiert. Die gestanzten Löcher erfüllen zudem den Zweck, den Stromfluss auch vertikal über mehrere Schichten zu ermöglichen und die spätere Befestigung der Leiterplatte zu erleichtern. Die Zusammenführung erfolgt unter Zuhilfenahme einer Presse, die neben Druck auch über Wärme eine Verknüpfung zwischen den einzelnen Teilbereichen herstellt.
Stabile Beschichtung
Um die Leiterplatte vor äußeren Einflüssen, die zu Korrosion oder Oxidation führen können, zu schützen, muss diese entsprechend beschichtet werden. Die Korrosionsschicht, die auch als Lötmaske bezeichnet wird, wird auf die Leiterplatte aufgetragen und mit UV-Wellen bestrahlt. Dies führt zu einer ersten Aushärtung der Lötmaske, die in einem zweiten Schritt durch eine zusätzliche Aushärtung im Ofen ergänzt wird. Abschließend erfolgt dann noch die Beschriftung der einzelnen Leiterplatten und der Funktionstest zur Qualitätssicherung.