Aluminium versus Stahl: Welche Rolle spielen moderne Legierungen im Karosseriebau?
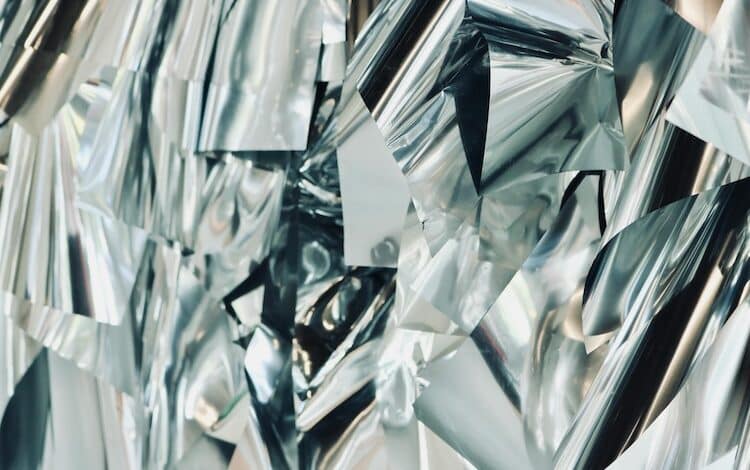
Im Karosseriebau stehen Aluminium und Stahl traditionell in Konkurrenz zueinander, doch die Entscheidung für das richtige Material ist komplexer geworden. Heutzutage kommen nicht mehr reine Metalle, sondern hochspezialisierte Legierungen zum Einsatz, die speziell auf die Anforderungen der Automobilindustrie abgestimmt sind. Während Stahl weiterhin aufgrund seiner hohen Festigkeit und Kosteneffizienz im Bereich tragender Strukturen dominiert, gewinnt Aluminium durch seine Leichtigkeit und Korrosionsbeständigkeit zunehmend an Bedeutung. Moderne Legierungen kombinieren die besten Eigenschaften beider Materialien und setzen neue Standards in Sachen Stabilität und Gewicht. Doch wann greift man auf Aluminium zurück, und wann bleibt Stahl das bevorzugte Material? Ein präziser Aluplatten-Zuschnitt ist zum Beispiel ideal für Anwendungen, bei denen hohe Flexibilität gefragt ist. Der Vergleich zeigt: Die Wahl des Materials bestimmt nicht nur die Leistungsfähigkeit, sondern beeinflusst auch die Wirtschaftlichkeit und Sicherheit eines Fahrzeugs maßgeblich.
Gewichtsersparnis im Fokus: Warum Aluminium bei modernen Fahrzeugkonzepten bevorzugt wird
Aluminium gilt in der Automobilbranche als Schlüsselmaterial für den Leichtbau. Mit einer Dichte von 2,7 g/cm³ ist es deutlich leichter als Stahl (7,85 g/cm³). Die Reduktion des Fahrzeuggesamtgewichts führt zu geringerem Kraftstoffverbrauch und reduzierten CO₂-Emissionen. Besonders in der Elektromobilität spielt das Gewicht eine entscheidende Rolle, da es die Batteriereichweite beeinflusst. Aluminium wird in Karosserieelementen wie Motorhauben, Türen und Dachrahmen eingesetzt. Auch in Fahrwerkselementen kommen zunehmend spezielle Legierungen zum Einsatz. Der Einsatz von Aluminium erfordert eine präzise Verarbeitung, wie sie etwa beim Aluplatten Zuschnitt notwendig ist. Trotz höherer Materialkosten amortisiert es durch gesenkte Betriebskosten und höhere Effizienz, besonders bei modernen Fahrzeugkonzepten, die auf Leichtbau ausgelegt sind.
Festigkeit und Flexibilität: Wie neue Legierungen die Grenzen von Aluminium und Stahl verschieben
Moderne Legierungen verschieben die Grenzen dessen, was bei Aluminium und Stahl möglich ist. Stahl überzeugt durch seine hohe Festigkeit, doch neue Aluminium-Magnesium-Silizium-Legierungen reduzieren dieses Defizit. Diese Legierungen erreichen in bestimmten Anwendungsbereichen Festigkeiten, die an hochfeste Stähle heranreichen. Gleichzeitig bleibt es flexibler und bietet eine bessere Energieabsorption bei Unfällen. Stähle wiederum entwickeln sich weiter: TRIP- und TWIP-Stähle kombinieren extrem hohe Zugfestigkeit und Formbarkeit. Solche Legierungen sind ideal für Bereiche, die starke Deformationen aushalten müssen, etwa die A- und B-Säulen eines Fahrzeugs. Die Wahl des Materials wird damit zur Frage, welche Legierung für den jeweiligen Anwendungsfall geeignet ist. Hybridkonstruktionen kombinieren die Vorteile beider Materialien, um Leichtbau und Sicherheitsanforderungen optimal zu erfüllen.
Kostenfaktor oder Innovationstreiber? Ein Blick auf die Wirtschaftlichkeit der Materialwahl
Bei der Entscheidung zwischen Aluminium und Stahl spielen Kosten eine zentrale Rolle. Stahl ist günstiger und lässt sich mit bewährten Fertigungstechniken effizient verarbeiten. Besonders bei Großserienproduktionen ist dieser Kostenvorteil nicht zu unterschätzen. Aluminium hingegen hat höhere Rohstoff- und Verarbeitungsaufwände, was die Herstellungskosten in die Höhe treibt. Doch allein die Materialkosten greifen zu kurz: Aluminium spart Treibstoff und senkt Verschleißkosten. Langfristig können die höheren Anschaffungskosten sich somit amortisieren. Neue Fertigungstechniken reduzieren den Aufwand und steigern die Produktionsgeschwindigkeit. Hochentwickelte Schweiß- und Fügetechniken für Aluminium senken den Zeitaufwand. Auch bei Stahl machen Warmumformungsverfahren die Verarbeitung von hochfesten Stählen effizienter. Die richtige Materialwahl ist immer eine Abwägung zwischen kurz- und langfristigen Kosten sowie den benötigten Eigenschaften.
Korrosionsbeständigkeit und Reparaturfreundlichkeit: Welches Material bietet langfristig die besseren Eigenschaften?
Aluminium ist für seine hohe Korrosionsbeständigkeit bekannt. Im Gegensatz zu Stahl bildet es eine schützende Oxidschicht, die es vor weiterem Verfall bewahrt. Stahl, selbst verzinkt, kann schneller rosten, wenn die Schutzschicht beschädigt wird. Man muss also genau überlegen, welches Material für die jeweiligen Umgebungsbedingungen am besten geeignet ist. Fahrzeuge in Gebieten mit hohem Salzgehalt oder extremen Wetterbedingungen profitieren von Aluminium. Im Reparaturfall zeigt sich jedoch, dass Stahl einfacher zu bearbeiten ist. Aluminium erfordert speziell geschultes Personal und spezielle Werkzeuge, was die Reparaturkosten steigen lässt. Hybridmaterialien aus Stahl und Aluminium setzen an dieser Problematik an und ermöglichen eine bessere Balance zwischen Korrosionsbeständigkeit und Reparaturfreundlichkeit. Hersteller sollten daher nicht nur die Materialeigenschaften bewerten, sondern auch die Folgen im After-Sales-Bereich berücksichtigen.